Track membranes, micro- and nanoporous materials
(On the series of research awarded second JINR Prize 2021 for Applied Research.)
The present-day field of nanotechnology is an extensive area that comprises a wide spectrum of approaches, utilising various physical and chemical principles and tools. Accelerated heavy ion beams are one type of tool for modifying materials and can function on the nanometre scale. There are two opportunities for transforming a material’s nanostructure by irradiation with high-energy heavy particles. First, nano-sized alterations can be produced through a direct effect on a crystal lattice due to energy transfer by elastic and inelastic collisions that occur in ion tracks. Secondly, a two-stage treatment can be applied, which includes the creation of local radiation damage followed by a chemical etching that leads to the formation of the final structure. Etching with heavy ion tracks is a well-known method of producing uniform micro- and nanopores in dielectrics. One of many practical applications of this method is the manufacture of microfiltration membranes (formerly called “nuclear filters”) implemented at the Flerov Laboratory of Nuclear Reactions in the mid-70’s.
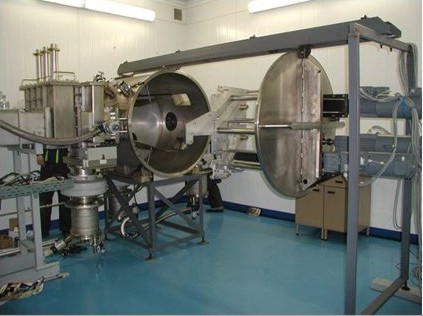
Fig. 1. Set-up for irradiating polymeric foils on the IC-100 accelerator: the vacuum chamber and web transport mechanism
At present, the research activity and the industrial-scale production of track membranes are based on the use of the heavy ion accelerators, U-400 and IC-100, equipped with specialised channels for the irradiation of polymer films. The ion-irradiated films are subject to subsequent physico-chemical treatment (sensitisation by ultraviolet radiation and chemical etching). A set of tools (scanning electron microscopy, various porometry methods) is used both for routine control over the quality of irradiation and the parameters of the track membranes (ТМs) that are produced, and for the current work aimed at the improvement of the TMs and the development of new nano- and micro-porous materials.
The use of the U-400 for materials modification started in the early 1990s. The cyclotron delivers beams of various ionic species from which krypton and xenon have been selected for routine irradiations of polymers. Typically, ion beams with energies of 2.5-5 MeV/u are employed. Depending on the specific application, the fluence accumulated in the target varies from about 104 to 1012 cm-2. In the last decade, a cyclic implanter IC-100 was put into operation at the FLNR. It belongs to a new generation of accelerators and is equipped with a superconducting ECR ion source and a system of external axial injections for the beam. This compact cyclotron with a 1 m pole diameter provides high-intensity beams of multiply charged ions of xenon, krypton, and argon with energies of 1.2 MeV/u. A system of beams scanning in two planes has been installed in the transport line of the extracted beam. It provides a homogeneous implantation of ions on a large area of the target (Fig. 1). Currently, the irradiation of polymeric materials is carried out by Kr15+ and Xe23+ ions that have a range of about 16 and 20 μm, respectively, in a polymer (e.g., polyethylene terephthalate). Therefore, the bulk modification of foils 10-20 μm thick and the surface modification of thicker materials can be performed on the IC-100.
Fig. 2. Cross-section of a PET TM with cylindrical parallel pores with a diameter of 0.8 μm (left) and with tilted (crossed) pores of the diameter of 0.3 μm (right). The thickness of the membranes is 10 and 12 μm, respectively. The first membrane was prepared for experiments on the propagation of ultrasonic waves through a porous medium. The second one is a conventional microfiltration ТМ used, for instance, for purifying drinking water.
The opportunities provided with the two accelerators mentioned above allow for the production of track membranes with a pore density in a range from 104 up to 3х109 cm2 and a pore diameter from 20 nm up to 5-7 μm (see examples in Fig. 2). A polyethylene terephthalate film (PET) serves as a raw material for the mass production of track membranes. However, for some special purposes, other materials can be successfully used. For example, polyimide and polyethylene naphthalate track membranes were developed for diffraction filters used in X-ray astronomy. A technology of manufacturing fluoropolymer TMs has also been developed. Various methods of surface and bulk modification, including production of composite track membranes have been suggested.